Case Study: Successful Implementation of Industrial Automation in a Melbourne Factory
Introduction to Industrial Automation
Industrial automation has become a pivotal component in modern manufacturing, driving efficiency and productivity. In a recent case study, a factory in Melbourne successfully implemented automation technologies, showcasing the transformative potential of these systems. This post delves into the key aspects of this implementation, highlighting the strategies and outcomes that marked its success.
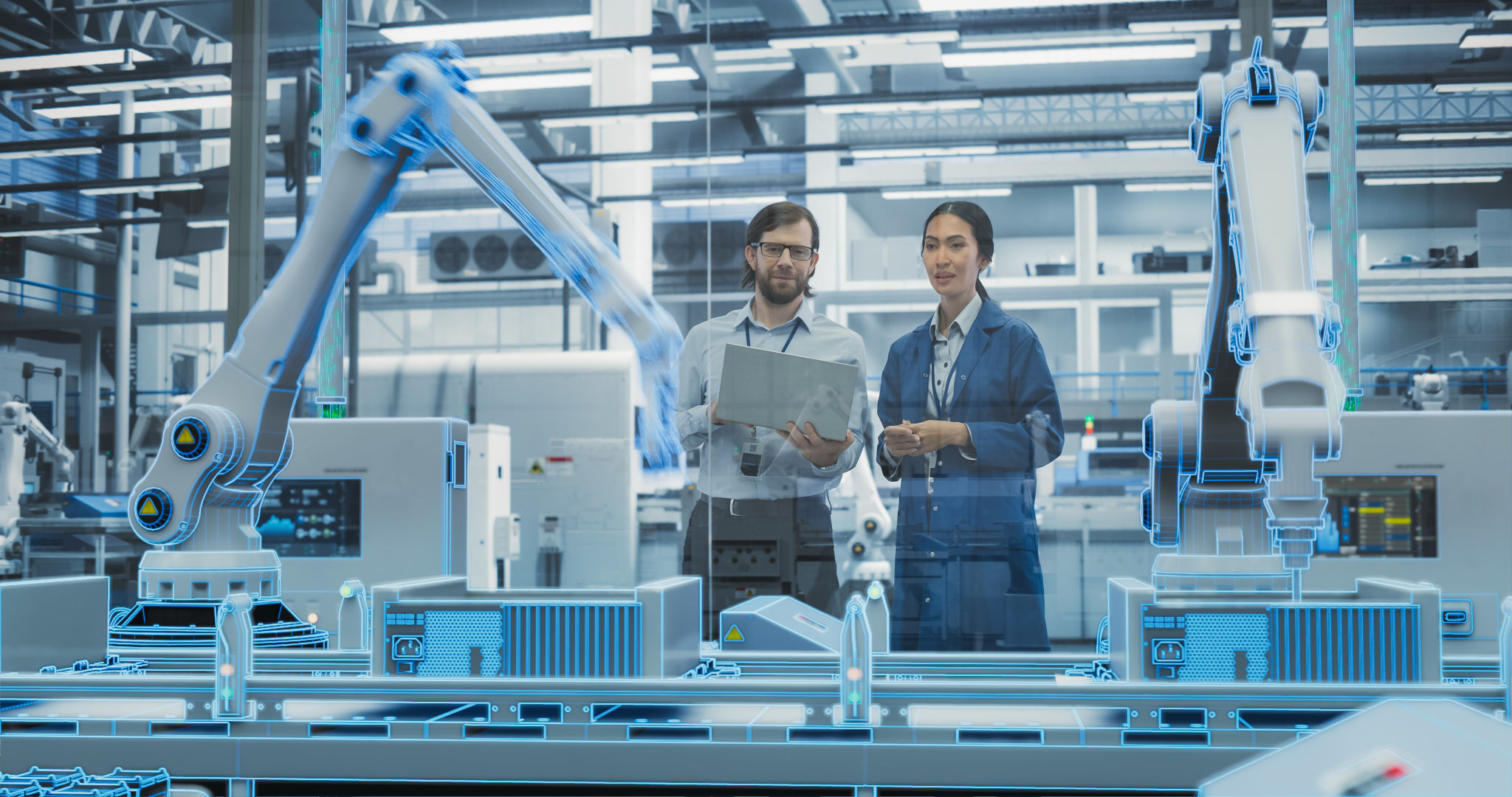
Understanding the Need for Automation
The Melbourne factory faced several challenges typical of traditional manufacturing environments, including high labor costs, inconsistent product quality, and inefficiencies in production processes. The decision to embrace automation was driven by the need to address these issues and enhance competitiveness in a rapidly evolving market.
By incorporating automated systems, the factory aimed to streamline operations, reduce human error, and improve overall output quality. The initial step involved a comprehensive analysis of existing processes to identify areas where automation could yield the most significant benefits.
Implementation Strategy
The implementation strategy was methodical and phased. The factory management began with pilot programs in critical areas, allowing them to test and refine automation systems before full-scale deployment. This approach minimized disruption and provided valuable insights into system integration and employee training needs.
- Phase 1: Assessment and Planning
- Phase 2: Pilot Implementation
- Phase 3: Full-Scale Rollout
- Phase 4: Continuous Improvement
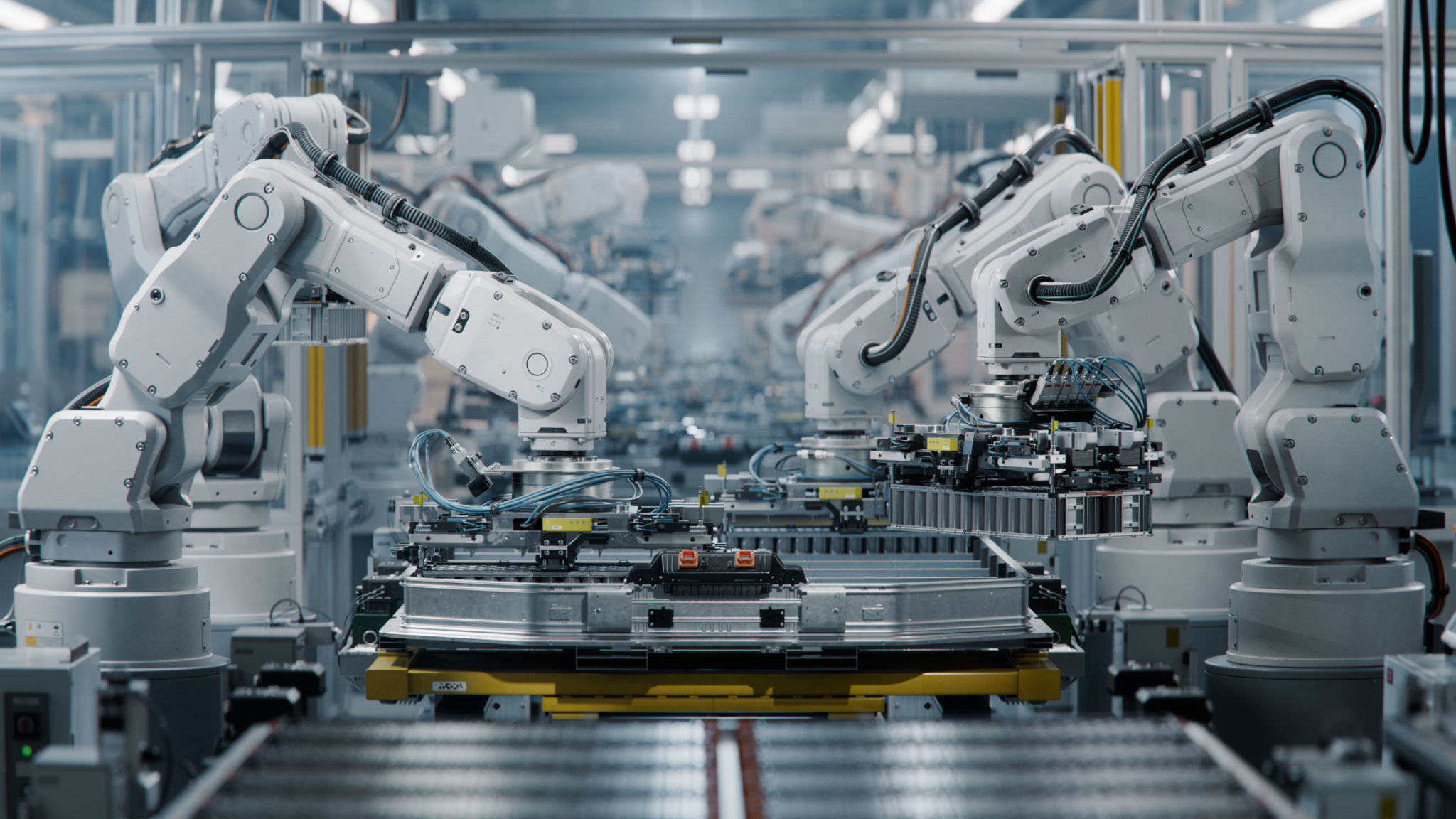
Technologies Employed
The factory leveraged several cutting-edge technologies, including robotic arms for assembly lines, AI-driven quality control systems, and IoT devices for real-time monitoring. These technologies were selected based on their ability to enhance specific aspects of production, such as speed, accuracy, and data collection.
The integration of IoT devices allowed for detailed tracking of production metrics, enabling data-driven decision-making that further optimized operations. By utilizing AI, the factory could predict maintenance needs and avoid costly downtime, significantly improving equipment lifespan and reliability.
Employee Training and Adaptation
A critical component of the automation project was ensuring that employees were adequately trained. The factory invested in comprehensive training programs to help staff adapt to new systems and workflows. This proactive approach not only facilitated a smoother transition but also boosted morale by involving employees in the innovation process.

Adapting to automation required a cultural shift within the organization. Management emphasized open communication and encouraged feedback from employees at all levels, fostering an environment of collaboration and continuous learning.
Measurable Outcomes
The results of the automation implementation were impressive. The factory reported a 30% increase in production efficiency and a 20% reduction in operational costs within the first year. Product quality improved markedly, with defect rates dropping by 15%, leading to higher customer satisfaction and increased market share.
Moreover, the factory's agility improved significantly, allowing it to respond more effectively to market demands and customer needs. These outcomes underscore the profound impact that well-executed automation strategies can have on manufacturing operations.
Conclusion
The successful implementation of industrial automation in this Melbourne factory serves as a compelling case study for manufacturers considering similar transformations. By strategically leveraging technology, involving employees in the process, and continually refining operations, the factory not only achieved its objectives but also set a benchmark for future endeavors.
As industries continue to evolve, embracing automation will be essential for maintaining competitive advantage and driving sustainable growth. This case study illustrates that with careful planning and execution, factories can harness the full potential of industrial automation.